Wie entsteht eigentlich Kunststoff?
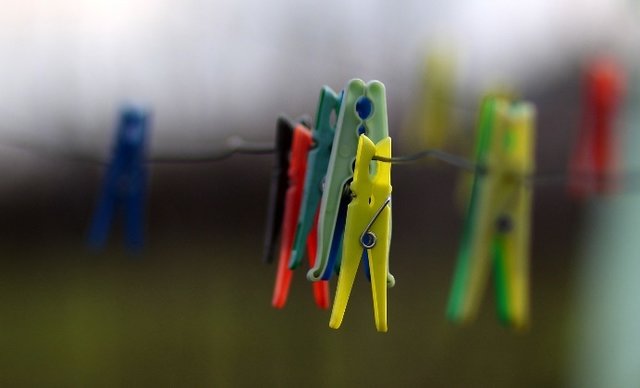
- Kunststoff hat unzählige Anwendungsbereiche. Und schon seine Herstellung ist ziemlich faszinierend.
- Foto: pixabay.com © AdinaVoicu
- hochgeladen von MarktSpiegel Service
SERVICE (se/fi) - Kunststoffe: Das Gerät, auf dem Sie diese Zeilen lesen, besteht wahrscheinlich weitestgehend daraus. Die Griffe unserer Küchenmesser auch. Und dazwischen eine Milliarde anderer Dinge zwischen der Verpackung Nürnberger Lebkuchen und Flugzeugrümpfen. Es gibt nicht nur viele unterschiedliche Kunststoffe, sondern sie müssen auch aufwendig hergestellt werden.
Viele verschiedene Arten von Kunststoffen
Kunststoff ist gleich Kunststoff? Von wegen! Tatsächlich fällt unter diesen Oberbegriff alles, was nicht unmittelbar so in der Natur vorkommt – dazu gehört dann beispielsweise auch Gummi, der aus erhitztem Kautschuk und Schwefel hergestellt wird. Im Rahmen dieses Artikels sollen aber „echte“ Kunststoffe beschrieben werden, also synthetische Polymere. Ohne tiefer auf deren hochkomplexe Chemie einzugehen, das sind Kunststoffe, die durch umfangreiche Zwischenprozesse ausgehend von Erdöl hergestellt wurden. Tatsächlich bestimmen unseren Alltag ein gutes Dutzend Kunststoffe, angefangen beim Polyethen/Polyethylen (PE) über Polystyrol (PS) bis zu Polyurethan (PU). Da sich aber die Herstellung teils dramatisch unterscheidet, beschränkt sich dieser Artikel aus Platzgründen auf den mit Abstand am häufigsten verwendeten Stoff, Polyethylen. Sie haben Frischhaltefolie in der Küche? Die besteht ebenso aus PE wie der Kunststoff-Mülleimer.
Aus dem Boden in die Küche
Das Kunststoffleben beginnt wie das unseres Autokraftstoffs, als Erdöl. Wie das gefördert wird, dürfte den meisten in Grundzügen bekannt sein. Interessanter ist jedoch das, was mit dem schwarzen Gold passiert, sobald es in der Raffinerie angekommen ist.
Dazu muss man sich eine Ölraffinerie wie einen Druckkochtopf auf einem Herd vorstellen – und das Erdöl als einen Wunderstoff, der unterschiedlichste Endprodukte enthält. Der Clou: Je nachdem, auf welche Temperatur man das Erdöl erhitzt, dampfen nur bestimmte Einzelteile davon aus. Ganz früh verflüchtigen sich Flüssiggase. Dreht man den „Herd“ etwas heißer, dampft Rohbenzin bzw. Naphtha aus. Noch mehr Wärme löst Otto-Benzin, Diesel und Heizöle heraus. Übrig bleibt eine schwarze, zähe Masse – Bitumen.
Rohbenzin oder Naphtha ist dabei die vielleicht wichtigste Grundlage unserer modernen Welt. Es enthält nämlich eine Menge wichtiger Kohlenwasserstoffe. Das Naphtha kommt nun in einen sogenannten Dampfcracker. Den kann man sich wie eine Art Brennofen vorstellen. Dort drin wird das Naphtha bei Temperaturen von bis zu 850°C „gecrackt“ oder aufgebrochen. Es entstehen neue, „kurzkettigere“ Kohlenwasserstoffverbindungen, darunter auch Ethylen bzw. Ethen. Und wer weiter oben genau gelesen hat, sieht schon, dass wir bereits dicht am Poly-Ethylen sind.
Eine Sache der Chemie
Ethylen wiederum ist einer der wichtigsten Grundstoffe für die gesamte Chemie. Denn es ist nicht nur unverzichtbare Ausgangsbasis für Kunststoffe, sondern darüber hinaus auch noch Tenside (unverzichtbar für Waschmittel), Reifungsgase in der Landwirtschaft und dazu noch für weitere Chemikalien, die ebenfalls in andere Produkte umgewandelt werden.
Allerdings: Mit dem Ethylen alleine lässt sich noch keine Frischhaltefolie herstellen. Dazu ist ein Prozess vonnöten, der als Polymerisation bekannt ist. Auch er lässt sich einfach erklären. Dazu stelle man sich die Ethylen-Bausteine wie einzelne, nicht verbundene Kettenglieder vor. Bei der Polymerisation geht es nun darum, diese Einzelglieder durch sehr hohe Drücke (wir sprechen hier von bis zu 4000 Bar) und Temperaturen um 200°C chemisch zu einer langen Kette umzuformen.
Dabei entsteht praktisch schon der Ur-Kunststoff, der Fachmann spricht von Polymerisat. Das ist ein weißes Pulver. Und ausgehend von diesem Pulver kann jetzt endlich die echte Kunststoffherstellung beginnen.
Etwas Wärme und Druck
Das Polymerisat ist zwar so gesehen fest, ließe sich aber ohne eine Zwischenstufe nur schwer zu Kunststoffen machen. Diese Zwischenstufe ist ein Extruder. In dieser Maschine wird das Pulver auf 200°C erhitzt und dadurch plastisch verformbar. So wird es dann durch Düsen gedrückt, die daraus endlos lange „Kunststoff-Fäden“ machen. Am anderen Ende steht eine Maschine, welche die Fäden in kleine Stücke unterteilt – reines Kunststoffgranulat.
Mit diesem Kunststoffgranulat kann man nun alles machen. In seinem Ursprungszustand ist es milchig-transparent. Für die eingangs erwähnte Frischhaltefolie ist das optimal, für andere Produkte eher weniger – soll das spätere Kunststoffprodukt farbig sein, so ist es notwendig, schon in der vorherigen Stufe das Polymerisat selbst durch Zugabe von Farbstoffen einzufärben. Aber: Ganz undurchsichtig wird PE kaum. Das kann man sehr schön sehen, wenn man ein beliebiges Produkt, das daraus entsteht, gegen das Licht hält. Nun wird es nochmal warm. Denn auch das Kunststoffgranulat kann dadurch, dass es erwärmt wird, abermals umgeformt werden.
Für diese Aufgabe haben die Ingenieure der vergangenen hundert Jahre eine ganze Menge Verfahren entwickelt, die alle ihren Einsatzbereich haben, je nachdem, was man aus PE herstellen möchte.
• Spritzgießen ist das häufigste Verfahren. Eine Spritzgießmaschine erwärmt dafür zunächst das Granulat und presst es dann unter höchstem Druck von bis zu 55.000kN in eine Form hinein. Dort erkaltet das flüssige PE wieder und behält seine endgültige Form.
• Blasformen muss man sich wie eine Kaugummiblase vorstellen. Dazu wird zunächst durch Spritzgießen ein sogenannter Vorformling erstellt. Eine Rohform, wenn man so will. Diese wird nun über eine Düse gestülpt, die wiederum von einer Form umschlossen, wird, welche der endgültigen Produktform entspricht. Nun wird der Rohling wieder erwärmt und „geblasen“. Dadurch dehnt er sich aus, bis er an die Wände seiner Form gepresst wird – so entstehen beispielsweise Kunststoffflaschen aus PE aber auch Frischhaltefolie.
• Formpressen kommt hauptsächlich bei großen, flachen Kunststoffbauteilen zum Einsatz, etwa Schneidbrettern aus PE für die Küche. Das Granulat wird dafür in großer Menge zu einem Klumpen verschmolzen. Der wird anschließend zwischen zwei riesige Pressformen gebracht und zu flachen Platten mit mehreren Metern Seitenlänge gepresst. Im letzten Schritt wird diese dann in einzelne Abschnitte zerteilt.
Zwar gibt es, alleine für PE, noch einige andere Verfahren. Diese drei sind jedoch, zusammen mit dem Extrudieren (zur Herstellung von Fasern) die am häufigsten verwendeten. Und das Beste: Durch Schreddern lässt sich jeder Kunststoff wieder so klein machen, dass er wieder und wieder recycelt werden kann. Daher gehört dieser Superstoff auch niemals in etwas anderes als die Recyclingtonne.
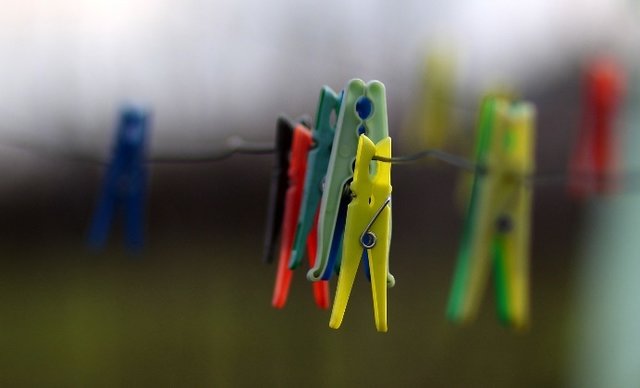
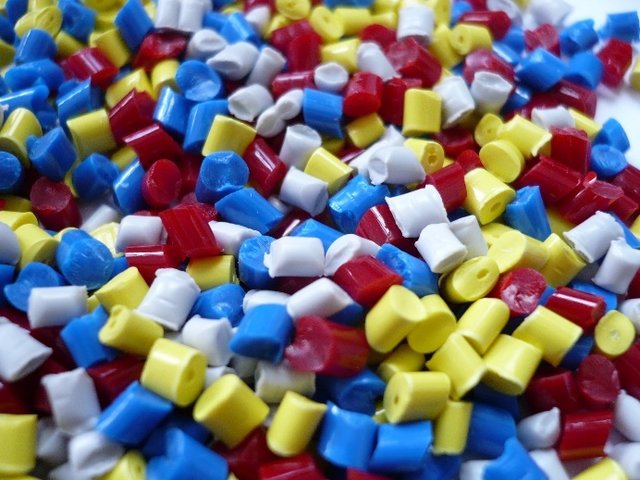
Autor:MarktSpiegel Service aus Nürnberg |
Sie möchten kommentieren?
Sie möchten zur Diskussion beitragen? Melden Sie sich an, um Kommentare zu verfassen.